Um fenômeno não detectável por exames convencionais de laboratório, mas que deteriora a mistura asfáltica e somente aparece sobre o pavimento depois de aberto ao tráfego
Fig.1
Há pouco tempo que na América Latina a preocupação com a qualidade da mistura asfáltica e sua expectativa de vida têm sido consideradas nos contratos de pavimentação e recuperação de estradas. Isto se deve, sem nenhuma dúvida, à introdução do conceito de Concessões Rodoviárias.
Isto significa que problemas inerentes ao processo DRUM MIX de produção da mistura asfáltica, até agora não observados pelos técnicos e especialistas em asfalto na América Latina, começam a ser notados no dia a dia por nossos empreiteiros. Todavia, estes problemas são conhecidos nos EUA há muitos anos e motivaram o desenvolvimento de novas tecnologias e equipamentos para superá-los, com vantagens mais do que concretas.
Neste trabalho, nos dedicaremos, especificamente, a um destes problemas - a destilação do cimento asfáltico no inter
Fig.1
Há pouco tempo que na América Latina a preocupação com a qualidade da mistura asfáltica e sua expectativa de vida têm sido consideradas nos contratos de pavimentação e recuperação de estradas. Isto se deve, sem nenhuma dúvida, à introdução do conceito de Concessões Rodoviárias.
Isto significa que problemas inerentes ao processo DRUM MIX de produção da mistura asfáltica, até agora não observados pelos técnicos e especialistas em asfalto na América Latina, começam a ser notados no dia a dia por nossos empreiteiros. Todavia, estes problemas são conhecidos nos EUA há muitos anos e motivaram o desenvolvimento de novas tecnologias e equipamentos para superá-los, com vantagens mais do que concretas.
Neste trabalho, nos dedicaremos, especificamente, a um destes problemas - a destilação do cimento asfáltico no interior do tambor misturador (Processo Drum Mix):
O processo Drum Mix é bastante simples e basicamente não sofreu nenhuma alteração desde a década de 70, quando foi introduzido nos EUA (Fig. 1). Os agregados úmidos previamente dosificados são introduzidos pelo mesmo lado do queimador e deslocam-se paralelamente à chama em cortinas sucessivas, de cima para baixo, formadas pelas palhetas levantadoras existentes no interior do tambor, que expõem a corrente de agregados a um contato direto com a chama, com o caudal de gases quentes provenientes da combustão e com uma forte corrente de ar fresco, necessária para arrastar para fora do tambor o vapor de água e a fumaça produzida no processo Drum Mix.
Entretanto, a simplicidade requer uma inter-relação definida e constante entre os três elementos chave do processo: 1- capacidade térmica do queimador (BTU/h); 2 - velocidade de avanço/exposição dos agregados (ton/h) e 3-capacidade de extração dos gases do interior do tambor (m3/h).
Estes três fatores, tomados como constantes dentro de um gradiente uniforme de temperatura horizontal na saída do tambor e em três pontos, pelo menos (Fig. 2), constituirão as duas curvas mestras da usina, como indicado na mesma Fig. 1.
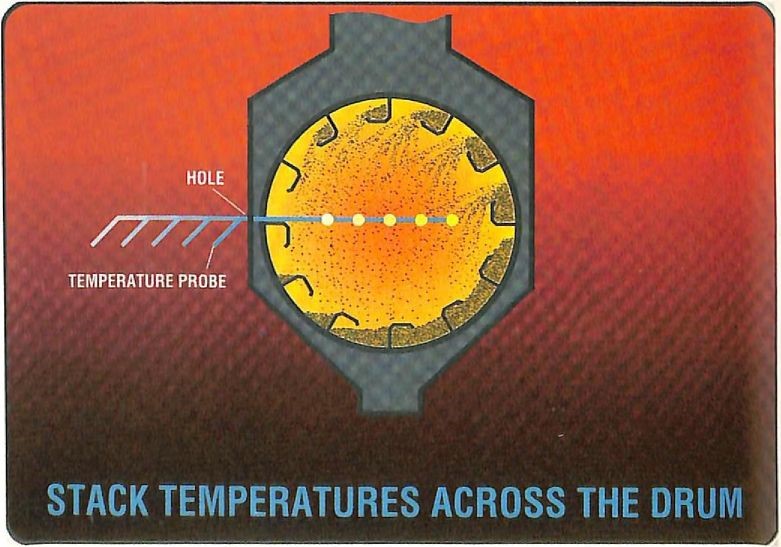
Fig.2 - Temperaturas de saída através do tambor
É importante ressaltar que a aspersão do asfalto no interior do tambor deve dar-se na zona onde tanto a curva de temperatura média dos gases quanto da temperaturamédia dos agregados começam a estabilizar-
se, o que ocorre em corno dos 150/160 °C
(Fig. 1).
É também importante notar que quando se acrescenta material reciclado (RAP) ao material virgem em processo, a curva de temperatura média dos gases mantém-se inalterada. Entretanto, a temperatura média dos agregados sofre variação considerável entre a zona de entrada do RAP e a zona de aspersão do asfalto (Fig. 3). Observe-se que
em ambos os casos a temperatura média de 150/160 °Cmantém-se constante na saída
da mistura/gases.
.jpg)
Fig. 3
A troca de apenas uma das variáveis acima pode modificar ambas as curvas mestras, levando-se em consideração que a magnitude da variação da curva dos gases é muito maior que a da curva dos agregados para o mesmo diferencial. Fica então claro que facilmente a temperatura da zona de aspersão do asfalto pode alcançar valores acima dos 300 °C (Fig. 1, curva adicional). Palhetas levantadoras mal projetadas de fabrica, mal recuperadas pelo próprio empreiteiro, posicionadas de forma errada, ou ainda desgastadas pelo uso, proporcionam uma temperatura muito desigual nos três
pontos da saída do tambor (Fig.4). Isto certamente aumenta exponencialmente a temperatura dos gases, ao mesmo tempo que aumenta, em alguns graus, a temperatura da mistura asfáltica. Da mesma forma, a localização do tubo de entrada do asfalto no interior do tambor também aspergirá em uma zona de altas temperaturas, trazendo como conseqüência odeterioro do cimento asfáltico. Trata-se aqui de procedimentos muito comuns entre os empreiteiros, que costumam fazê-los a fim de aumentar o tempo de mistura e “melhorar” a qualidade da mesma, o que é, evidentemente, falso.
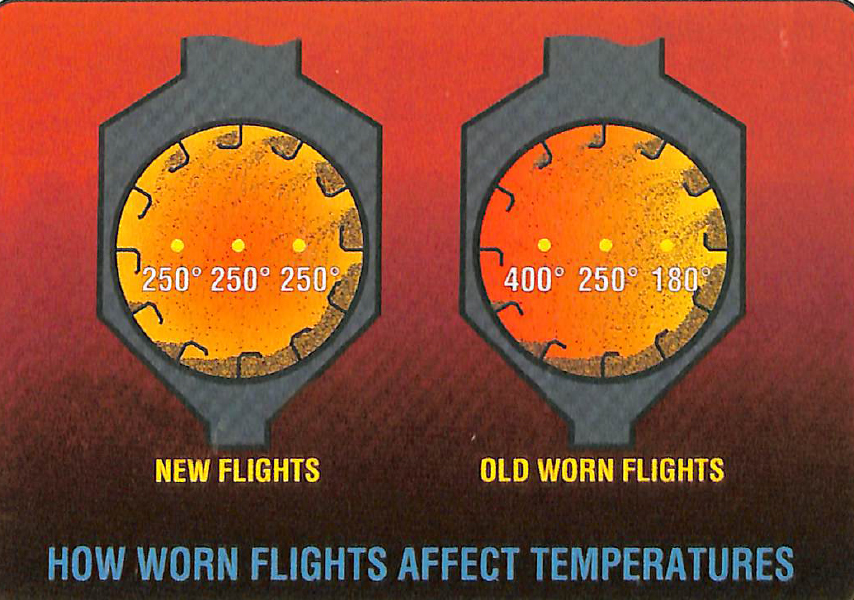
Fig. 4 - Como as palhetas desgastas afetam as temperaturas
Considerando-se, também, que a grande maioria de nossos empreiteiros não monitoram a temperatura da chaminé do exaustor de gases (Filtro de Mangas, Filtro úmido e Filtro seco), perde-se uma valiosa ferramenta de controle da qualidade do processo, da usina e da mistura. (Nossacultura requer apenas o controle de temperatura da mistura na saída da usina). Uma vez compreendido o que apresentamos acima, passaremos agora a fazer uma análise do comportamento do cimento asfáltico durante o processo de mistura dentro do tambor Drum Mix:
Como se sabe, o asfalto é o produto final do óleo cru e sua viscosidade depende do grau API do cru processado (Fig. 5). Antes da crise do petróleo de 1974, os asfaltos produzidos nas refinarias eram distribuídos ao mercado com suas viscosidade naturais, mas os esforços para baratear os preços dos derivados de petróleo fizeram com que o asfalto, sofresse uma redução dos poucos elementos nobres dissolvidos nele. Desde então, a fim de adequar sua viscosidade ao requerido pelo projeto da mescla, voltou-se a acrescentar parte dos óleos leves anteriormente retirados durante o processo de destilação fracionada.
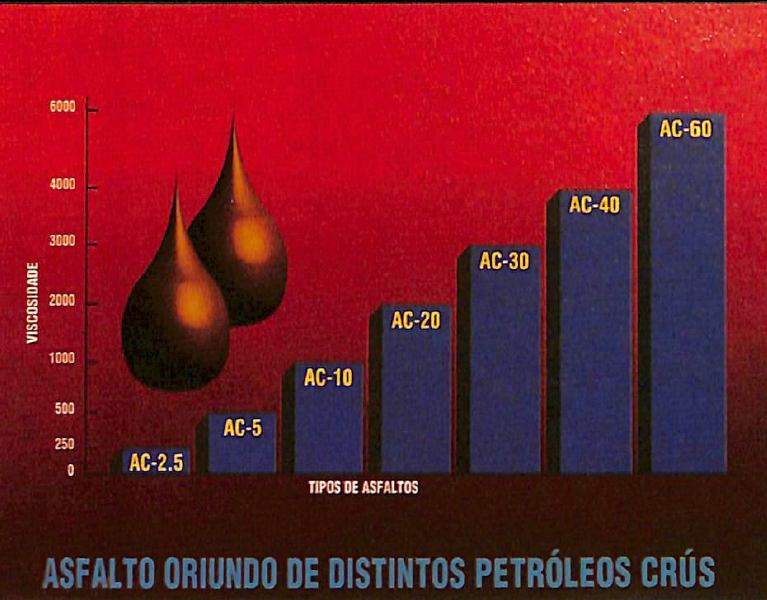
Fig.5
Deve-se também levarem consideração que durante o moderno processo de destilação na refinaria se injeta ao cru vapor d’água a temperaturas entre 380°C e 450°C, e o asfalto sai da coluna de destilação a aproximadamente 320°C (Fig. 6). Suponhamos agora que os agregados que estamos processando em nossa usina Drum Mix tenham uma umidade atípica (por exemplo, 9%, 10% ou mais), como acontece nas épocas de chuva.
Fig.6
Suponhamos também, que nossa usina tenha todas, ou parte, das imperfeições acima, de forma que a temperatura da zona de aspersão do asfalto seja igual ou superior aos 300°C:
Isto significa que teremos os elementos mínimos necessários para reproduzir, no interior do tambor, parte da coluna de destilação do óleo cru (!), o que a usina fará automaticamente, enquanto produz a mistura asfáltica.
Uma vez estabelecido o processo de destilação parcial no interior do tambor, uma pequena parte destes óleos leves é arrastada para o filtro de mangas, encharcando-as a ponto de causar uma explosão. Isto se nota nos escorrimentos nos dutos anteriores ao filtro assim como na chaminé.
No Brasil e nos países latino-americanos existem vários fabricantes locais de filtros de mangas que incorporaram a seus filtros uma tecnologia curiosa e ineficiente - uma tomada de ar fresco no duto entre o tambor Drum Mix e o filtro de mangas que costuma abrir-se automaticamente caso a temperatura dos gases no interior do filtro ultrapasse um determinado valor, que ponha em risco os filtros de algodão (em poucos casos utiliza-se os de Nomex). Normalmente estes aparelhos estão ajustados para uma temperatura bastante baixa, para proteger os filtros de algodão (mais baratos que os de Nomex), de forma que os filtros de mangas operam, quase sempre, com a tomada de ar fresco aberta. Isto faz com que a velocidade dos gases quentes no interior do tambor diminua, tendo como conseqüência um considerávelaumento da temperatura. Este quadro cria as condições ideais para que se produza a destilação do cimento asfáltico (!).
Ainda como conseqüência, algumas zonas no interior do filtro de mangas poderão estar com a temperatura dos gases inferior ao Ponto de Condensação (Dew Point), causando aderência de pó na base e paredes do filtro, que por sua vez, requerem paradas constantes da usina para limpeza.
Quando se trata de um filtro úmido, os problemas de operação são menos complexos, mesmo assim pode-se observar uma camada de óleo na superfície d’água. São os óleos leves resultantes da destilação do cimento asfáltico. No meio costuma-se dizer, erroneamente, que estes óleos no tanque de decantação provêem de “um combustível mal queimado”. Isto não ocorre quando se trabalha com queimadores eficientes e bem ajustados, do contrário, é possível que aconteça quando se trata de queimadores velhos, ineficientes e com a relação ar/combustível inadequada. Convém relembrar que “este combustível mal queimado” incorpora-se também à mistura e só o excesso será acrescentado aos óleos leves destilados no tanque de decantação. Quando se trata de filtros secos (de ciclone) pode-se observar a destilação do cimento asfáltico através do escorrimento de óleo na chaminé e na tubulação do exaustor.
Deve ficar claro que, a maior parte destes óleos leves recobre os áridos, como o asfalto, agora mais duro após a destilação,mas deforma diferente. Visualmente não se nota que ambos produtos estejam recobrindo separadamente os agregados da mistura.
Agravando ainda mais o problema, os ensaios convencionais delaboratório para detectar o teor de asfalto na amostra de mistura, antes ou depois de compactada, indicarão valores corretos, já que o método de“lavagem” aplicado, com solventes potentes e voláteis, como o tricloroetileno, dissolverá tanto o asfalto mais duro como os óleos leves que convivem separadamente na mesma amostra. Oresultado final de laboratório será muito coerente com as especificações.
Na prática, assim que o asfalto comece a sofrer as exigências do tráfego, apresentará rachaduras precoces por fadiga e até uma exsudação esquisita, onde o material exsudado emulsiona-se com as chuvas produzindo uma substancia de aspecto leitoso.
Um simples exame de laboratório confirmará que se trata de óleo leve e água. Tal fenômeno, por ser desconhecido, costuma originar outros problemas que um profissional de construções rodoviárias ja deve ter encontrado ao longo de sua atuação profissional, não sabendo explicá-los de forma convincente e racional.
Convém destacar que este foi um dos vários motivos que levaram a Astec, a partir de 1977, a se dedicar à busca de uma solução econômica e definitiva para este problema específico, assim como para vários outros que surgiram ao longo dos anos. Alguns exemplos das necessidades são o crescente uso do RAP (Pavimento Asfáltico Reciclado); asfalto polimérico com SBS; Superpave; o sistema SHRP; as misturas de granulometria aberta autodrenante; Stone Matrix, etc. que requerem maior tempo de mistura e garantia constante de qualidade.
Outras famílias de usinas de asfalto de tambor foram desenvolvidas pela Astec a fim de substituir o Drum Mix (Fig- 7. fig. 8 e Fig. 9), antes de chegar à solução definitiva através do DOUBLE BARREL,em 1989 (Fig. 10).
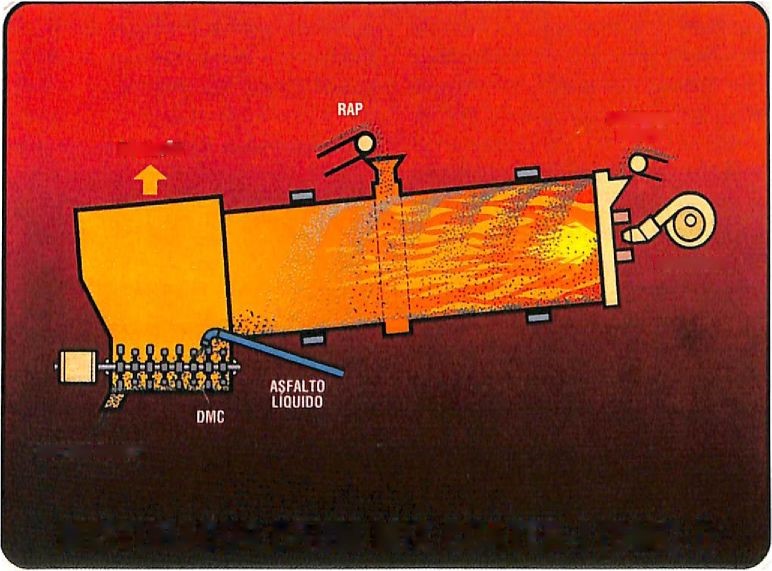
Fig.7
Fig.8
Fig.9
Bibliografia:
Astec’s Teehnical Paper T-126 - Productivity - J. Don Brock, PhD., P.E. John Milsted, BSME
Astec’s Teehnical Paper T-119 - DRYERDRUM MIXER-J. Don Brock, PhD.,PE